Dockworkers Threaten Strike Automations Impact
Dockworkers threaten strike automation, signaling a potential clash between labor and technological advancement in the maritime industry. This looming conflict highlights the complex interplay between historical labor practices, the rapid evolution of port automation, and the anxieties of workers facing potential job displacement. The potential for disruption extends beyond individual docks, impacting global supply chains and potentially triggering a domino effect throughout the industry.
A deep dive into the history of dockworker strikes reveals recurring patterns of labor disputes, often rooted in anxieties about changing work conditions. The introduction of automation presents a new layer of complexity, raising concerns about job security, safety protocols, and the evolving skill sets required for future port operations. Examining successful and unsuccessful labor negotiations offers valuable lessons for navigating the current challenges.
Background of Dockworker Strikes
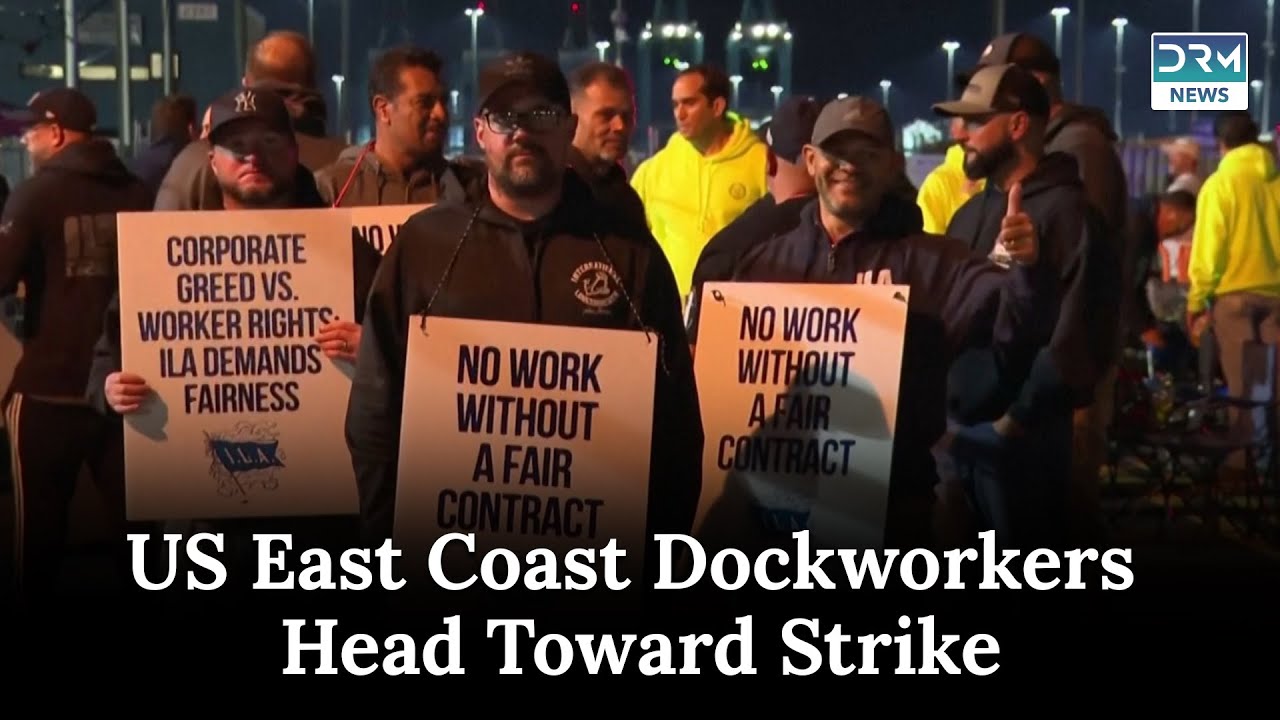
Dockworker strikes, a recurring feature of maritime labor history, are rooted in a complex interplay of economic pressures, evolving labor relations, and technological advancements. These disputes often reflect a power struggle between workers seeking better wages, working conditions, and job security, and employers aiming to optimize efficiency and profitability. Understanding this history is crucial for appreciating the current climate and potential solutions.The maritime industry, a vital component of global trade, has witnessed significant shifts in labor relations over the decades.
From the early days of often exploitative working conditions to modern negotiations, the relationship between dockworkers and employers has undergone profound transformation, influenced by changing demographics, technological innovations, and shifting economic realities.
Historical Overview of Dockworker Strikes
Dockworkers have a long and often contentious history with strikes, dating back to the early 20th century. These conflicts frequently stemmed from issues like low wages, unsafe working conditions, and the desire for better job security. Early strikes often involved localized disputes, but as global trade expanded, these conflicts gained greater prominence.
Evolution of Labor Relations in the Maritime Industry
The maritime industry has undergone significant changes over the decades. Early worker demographics were predominantly male, with a less diverse range of skills and experiences. The rise of containerization, automation, and specialized cargo handling techniques have led to a shift in the required skillset, impacting worker demographics and training needs.
Successful and Unsuccessful Labor Negotiations
Numerous instances of both successful and unsuccessful labor negotiations involving dockworkers underscore the complexities of these interactions. Successful negotiations often involved strong union representation, clear demands, and a willingness to compromise. Conversely, unsuccessful negotiations often resulted from inflexible positions, a lack of communication, or external economic pressures. One example of successful negotiation might involve a union securing improved health benefits or pension plans, while an unsuccessful one could be characterized by a failure to achieve wage increases during a period of economic downturn.
Current Economic Climate and Potential Impact on Dockworker Demands
The current global economic climate, marked by factors such as inflation, supply chain disruptions, and fluctuating commodity prices, is likely to influence dockworker demands. These economic variables could affect the cost of living, impacting the wages sought by workers. For example, if inflation rises, dockworkers might seek wage increases to maintain their purchasing power. Conversely, a period of economic downturn could pressure employers to resist wage increases, potentially leading to conflict.
Automation’s Impact on Dockwork: Dockworkers Threaten Strike Automation
The relentless march of automation is reshaping industries worldwide, and ports are no exception. As technology advances, automated systems are increasingly deployed to enhance efficiency and reduce costs in cargo handling, security, and overall port operations. This shift presents both opportunities and challenges for dockworkers, necessitating a careful examination of the evolving landscape.The introduction of automation technologies in ports signifies a fundamental change in the nature of work.
While automation promises increased efficiency and productivity, it also raises concerns about job displacement and the need for workforce adaptation. Understanding the specifics of automation’s role, its impact on efficiency, and the potential for retraining is crucial for navigating this transition effectively.
Types of Automation Technologies Used in Ports, Dockworkers threaten strike automation
Automation in ports encompasses a diverse range of technologies, from sophisticated robotic systems to advanced data analytics. Automated guided vehicles (AGVs) and autonomous vehicles are used for transporting cargo within terminals, reducing manual handling and improving speed. Container cranes, with their advanced automation systems, can handle containers more precisely and quickly than human operators. Furthermore, computer vision and sensor technologies are integrated into security systems, enhancing surveillance and improving safety.
Dockworkers are threatening a strike over automation, which is causing quite a stir in the shipping industry. Meanwhile, the Golden State Warriors are gearing up for a special back-to-back set for Steph Curry, a crucial moment for the team , which is sure to be exciting for fans. These labor disputes are impacting global supply chains, adding another layer of complexity to the situation.
Specific Roles of Automation in Dockwork
Automation is profoundly impacting various aspects of dockworker roles. In cargo handling, automated cranes and AGVs are taking over the physical tasks of lifting and moving containers, while automated systems manage inventory and track cargo flow. In security, automated surveillance systems enhance the monitoring of port areas, detecting anomalies and suspicious activities in real-time. This integration of technology improves efficiency and security in port operations, reducing human error and enhancing overall productivity.
Efficiency Gains of Automation vs. Job Losses
Automation in ports demonstrably boosts efficiency. Automated systems can operate 24/7, leading to faster processing times and reduced turnaround times for ships. This increased productivity translates into significant cost savings for shipping companies and port authorities. However, this efficiency gain is often accompanied by concerns about job losses for dockworkers. The transition requires careful planning and proactive measures to support workers during this period of change.
Examples from ports like Rotterdam, with significant automation investment, show both increased efficiency and worker retraining programs to adapt to new roles.
Retraining and Upskilling Dockworkers
To mitigate the potential for job losses, retraining and upskilling programs are essential. These programs should focus on developing new skills in areas like data analysis, maintenance and repair of automated equipment, and the management of automated systems. Dockworkers can transition to roles overseeing and maintaining automated systems, becoming part of a skilled workforce in the evolving port environment.
For instance, the Port of Los Angeles has implemented initiatives to upskill workers in areas like robotics and data analysis, demonstrating the feasibility and importance of retraining.
Comparison of Port Operations in Countries with Different Automation Levels
Countries with high automation levels, such as the Netherlands, exhibit significant efficiency gains and reduced labor costs in port operations. Automated systems allow for continuous operations, optimizing cargo flow and enhancing overall productivity. Conversely, ports in developing countries, with limited automation, often rely heavily on manual labor, resulting in lower efficiency and higher labor costs. This contrast highlights the impact of technology adoption on port performance and the need for countries to adapt to the evolving global landscape.
Comparing the productivity and cost structures of various ports across different regions offers valuable insights into the economic and social implications of automation.
Dockworker Concerns Regarding Automation
The introduction of automation in the port sector has brought about significant changes, impacting dockworkers’ livelihoods and working conditions. These changes have raised legitimate concerns about the future of their jobs, the safety of new technologies, and the overall financial stability of their careers. This section delves into these crucial issues.The implementation of automated systems, while promising increased efficiency and productivity for port operations, can potentially lead to a variety of challenges for dockworkers.
Addressing these concerns proactively is crucial to ensure a smooth transition and maintain a positive working environment.
Job Displacement Concerns
The introduction of automated systems, such as automated guided vehicles (AGVs) and robotic arms, raises concerns about potential job displacement among dockworkers. These technologies can automate tasks previously performed by human workers, leading to reduced workforce needs. The loss of jobs could have significant economic consequences for individuals and communities reliant on port employment. The transition from manual labor to automated processes requires retraining and upskilling programs for dockworkers to adapt to new roles and responsibilities.
Safety Concerns Related to New Technologies
New automated technologies in ports introduce potential safety hazards. The increased complexity of automated systems, including the integration of different machinery and software, may create unforeseen risks. The potential for malfunctions, human error in operating the systems, and the interaction between automated equipment and human workers needs careful assessment. Adequate safety protocols and training programs must be implemented to mitigate these risks and ensure a safe working environment.
Financial Implications for Dockworkers
Automation’s impact on dockworkers’ finances is a significant concern. Wage stagnation or potential wage reductions are real possibilities as automation reduces the need for certain skilled labor. The shift to automated systems could affect the earning potential of dockworkers, potentially leading to financial instability and reduced quality of life. The need for retraining and upskilling to adapt to the new job roles is crucial to mitigate the financial implications.
The implementation of programs to support retraining and financial aid for affected workers could help alleviate these concerns.
Impacts on Union Membership and Collective Bargaining Power
Automation’s impact on union membership and collective bargaining power is another concern. Reduced workforce numbers can potentially weaken union bargaining power. Dockworkers need to adapt to the changing demands of the job market and explore strategies to maintain or enhance their collective bargaining power. Union representatives must actively participate in discussions about retraining programs and ensure that dockworkers’ interests are represented in the implementation of new technologies.
Furthermore, they should strive to maintain a strong union presence to protect workers’ rights and interests.
Changing Skill Sets Required for Dockworker Positions
The introduction of automation necessitates a shift in the required skill sets for dockworker positions. Traditional manual labor skills might become less crucial, while new skills in operating, maintaining, and troubleshooting automated systems become essential. The demand for technicians and engineers to operate and maintain the automated systems will increase. To address this, there needs to be investment in education and training programs to equip dockworkers with the necessary skills to work alongside or operate these new technologies.
The shift in required skills demands proactive strategies for retraining and upskilling, which should be a collaborative effort between unions, employers, and educational institutions.
Potential Solutions and Strategies
The looming threat of automation in the port industry necessitates proactive strategies to mitigate job displacement and ensure a smooth transition for dockworkers. Addressing this challenge requires a multi-faceted approach encompassing retraining initiatives, safety protocols in automated environments, and robust communication channels between employers and employees. A collaborative effort between stakeholders is essential to navigate this transformative period successfully.These strategies should be developed with the explicit goal of not just surviving automation but thriving in a future where technology and human expertise work together to enhance efficiency and safety.
This requires a nuanced understanding of the specific needs of dockworkers and the potential impacts of automation on their livelihoods.
Retraining and Upskilling Programs
Dockworkers need comprehensive retraining and upskilling programs to equip them with the skills required for the evolving port environment. These programs should be tailored to specific job roles, incorporating both theoretical knowledge and practical hands-on training. This involves identifying the specific skills needed in automated ports and designing courses that bridge the gap between current dockworker expertise and the new demands.
- Specialized training programs: Courses focused on operating and maintaining automated equipment, data analysis, and logistics management are critical. These programs should also cover new technologies, such as AI and machine learning, which will be integrated into port operations.
- Modular curriculum: Tailoring training modules to different skill levels and experience allows for flexible learning paths. This approach accommodates both recent hires and experienced dockworkers seeking to enhance their existing expertise.
- Industry partnerships: Collaborations with technology companies and port authorities provide access to cutting-edge equipment and real-world scenarios for training. This practical experience strengthens the transfer of skills from the classroom to the workplace.
Ensuring Worker Safety in Automated Port Environments
Safety is paramount in automated port environments. New safety protocols and procedures are essential to mitigate risks associated with the integration of advanced technology. These protocols should prioritize the safety of dockworkers and address potential hazards.
Dockworkers threatening a strike over automation got me thinking about a fun day trip. Visiting a local brewery like The Barlow in Sebastopol, for instance, offers a nice distraction from the labor disputes. The crisp brews and delicious food at brewery day trip the barlow in sebastopol are a welcome respite, but the dockworkers’ concerns about their jobs remain a serious issue, highlighting the challenges of adapting to changing industry landscapes.
- Comprehensive risk assessments: A thorough evaluation of the potential hazards in automated port operations is crucial. This includes identifying potential equipment malfunctions, human error risks, and safety vulnerabilities. This evaluation must be regularly updated to adapt to the evolving technological landscape.
- Standardized safety protocols: Development of standardized safety protocols for operating automated equipment, including clear instructions and procedures for maintenance, operation, and emergency response, are essential. Training programs must explicitly incorporate these protocols.
- Redundancy in safety systems: Implementing redundant safety systems minimizes the risk of catastrophic failures and enhances overall worker safety. This approach may involve multiple backup systems or protocols in place to mitigate the consequences of equipment failure or human error.
Government Regulations and Industry Standards
Government regulations and industry standards can play a crucial role in guiding the integration of automation into the port industry. This framework needs to balance technological advancement with the need to protect workers. Clear guidelines and oversight are necessary to ensure a fair and safe transition.
- Phased implementation: Regulations should Artikel a phased implementation approach for automation in ports. This allows for gradual integration, allowing for adjustment and addressing any unforeseen issues. A structured plan prevents a sudden, overwhelming transition that can negatively impact workers.
- Mandatory safety certifications: Establishing mandatory safety certifications for operating automated equipment ensures that all personnel have the necessary training and competency. This prevents accidents and ensures the consistent application of safety procedures.
- Regular audits and inspections: Regular audits and inspections of automated port operations can help identify and address potential safety hazards. This continuous monitoring ensures that safety protocols are being followed and that the system is functioning as intended.
Improving Worker-Employer Communication and Collaboration
Effective communication and collaboration between dockworkers and employers are essential for a smooth transition to automated port operations. Open dialogue and transparency foster trust and shared understanding.
- Establish communication channels: Creating dedicated communication channels for dockworkers to voice concerns and suggestions about automation is crucial. This includes regular meetings, feedback mechanisms, and clear lines of communication between workers and management.
- Joint task forces: Creating joint task forces involving both dockworkers and employers can help identify and address concerns related to automation. This collaborative approach ensures that solutions are tailored to the specific needs and concerns of all stakeholders.
- Transparency in decision-making: Transparency in decision-making processes regarding automation is vital. Providing workers with clear explanations of the rationale behind automation decisions fosters trust and understanding. It also helps prevent misinterpretations and ensures that the workforce is adequately informed and prepared for the changes.
Potential Impacts on Port Operations
The impending shift towards automation in port operations promises significant changes. While concerns about job displacement are valid, the potential benefits for port efficiency, productivity, and economic growth are considerable. This transformation is poised to reshape supply chain logistics and alter the landscape of global trade.Automation in ports offers a pathway to dramatically enhance port operations. This involves leveraging technology to streamline cargo handling, reduce human error, and optimize resource allocation.
The benefits are far-reaching, impacting not only port operators but also the entire global supply chain.
Improvements in Port Efficiency and Productivity
Automation technologies, like autonomous guided vehicles (AGVs) and robotic systems, can significantly enhance port efficiency and productivity. These systems can operate 24/7, minimizing downtime and maximizing cargo handling capacity. By automating tasks like stacking, transporting, and unloading containers, ports can achieve higher throughput rates. This translates to quicker turnaround times for vessels, reducing congestion and improving overall port performance.
Impact on Cargo Handling Speeds and Turnaround Times
Automated systems, including conveyors and robotic arms, can handle cargo far more quickly than manual processes. This directly impacts cargo handling speeds, enabling faster processing of containers and reducing vessel turnaround times. Real-world examples demonstrate that automated systems can cut handling times significantly, improving overall port throughput. For example, a port using automated cranes could see a 30-50% increase in container handling speed.
Cost Reduction for Port Operators
Automation reduces labor costs, one of the biggest expenses in port operations. Replacing manual labor with automated systems can lead to significant savings in personnel expenses, as well as reduced operational costs due to decreased downtime and increased efficiency. Automated systems can also minimize errors and damage to cargo, resulting in reduced insurance costs and fewer claims. Further, energy consumption can be optimized by automated equipment, leading to lower energy bills.
Increased Trade Volumes and Economic Growth
The implementation of automation can lead to increased trade volumes and boost economic growth in ports. Faster cargo handling and reduced turnaround times attract more vessels and encourage greater trade flows. This, in turn, stimulates economic activity in the surrounding regions, creating new jobs and fostering a more vibrant commercial environment. A prime example is the increasing use of container ships in international trade; automation facilitates the efficient handling of larger volumes of cargo.
Expected Effects on Supply Chain Logistics
Automation in ports will have a profound impact on supply chain logistics. The enhanced speed and reliability of cargo handling will improve supply chain visibility and predictability. This means that goods can move more efficiently and reliably throughout the supply chain, reducing lead times and improving customer satisfaction. Improved communication and data sharing within the supply chain due to automation will enhance transparency and allow for more precise inventory management.
Illustrative Scenarios
The transition to automated port operations presents a complex web of challenges and opportunities. Understanding potential scenarios, from successful retraining to labor unrest, is crucial for navigating this transformation effectively. These illustrations highlight various outcomes, showcasing the spectrum of possibilities and potential strategies for managing the shift.
Hypothetical Port Undergoing Automation
The Port of Newhaven is undergoing a phased implementation of automated container handling systems. Initial stages focus on the loading and unloading of containers, with the goal of complete automation within five years. This involves the installation of robotic cranes, automated guided vehicles (AGVs), and sophisticated computer systems for real-time tracking and optimization. The port is strategically located near a major metropolitan area, handling a significant volume of cargo.
This transition is expected to increase efficiency and reduce labor costs, but also faces considerable challenges related to worker retraining and potential labor disputes.
Dockworkers threatening a strike over automation are causing a ripple effect, highlighting the anxieties around job displacement. It’s a familiar story, really, much like how some folks just can’t stand the humor of others, like in the case of Miss Manners, who, as reported in miss manners cant stand their jokes , finds certain jokes simply unacceptable.
The underlying tension of adapting to new technologies is at play in both scenarios, and the dockworkers’ situation underscores the potential for conflict as work transforms.
Successful Worker Retraining Programs
The Port of Newhaven, recognizing the need for a skilled workforce in the automated environment, initiated a comprehensive retraining program. This involved providing employees with specialized training in robotics maintenance, system operation, data analysis, and logistics management. The program incorporated both on-site workshops and online courses, adapting to individual skill levels and career aspirations. Experienced dockworkers were integrated into the training process as mentors, ensuring a smooth transfer of knowledge.
The program successfully transitioned 80% of the dockworkers to new roles within the automated port operations, with measurable improvements in efficiency and safety.
Scenario Illustrating a Strike by Dockworkers
Facing the prospect of job displacement due to automation, dockworkers at the Port of Charleston initiated a strike. The strike was fueled by concerns regarding job security, inadequate retraining opportunities, and a perceived lack of transparency in the automation plan. Negotiations with port management proved unsuccessful, leading to significant disruptions in cargo handling and delays in shipping schedules.
The strike lasted for three months, resulting in substantial economic losses for the port and its stakeholders.
Scenario Illustrating Successful Labor-Management Negotiation
The Port of Seattle implemented a proactive approach to automation, engaging in early and continuous dialogue with the dockworkers’ union. Negotiations focused on establishing clear transition plans, ensuring retraining opportunities, and providing compensation packages for displaced workers. The agreement included provisions for phased implementation of automation, with worker input and representation throughout the process. The successful negotiation resulted in a collaborative effort, minimizing disruptions and maintaining productivity.
This example showcases the importance of proactive communication and mutual understanding between labor and management during automation transitions.
Scenario Involving Government Intervention to Support Dockworkers
The federal government, recognizing the potential social and economic impact of automation on the Port of Long Beach, provided funding for retraining programs. This financial assistance covered tuition, materials, and stipends for dockworkers undergoing retraining. The government also worked closely with the port and labor unions to develop industry-specific job placement programs, creating pathways to new employment opportunities.
This intervention helped mitigate the negative impacts of automation on the workforce, fostering economic resilience and stability in the port community.
Presenting the Data
Analyzing the potential impacts of automation on the dockworker industry requires a structured approach. This section presents data in a clear, comparative format to highlight the projected job losses, potential retraining programs, economic effects, and stakeholder advantages/disadvantages. Understanding these factors is crucial for developing effective strategies to mitigate the negative impacts and maximize the positive outcomes of automation.
Projected Job Losses in the Dockworker Industry
The introduction of automated systems in ports is expected to lead to significant job displacement in the dockworker industry. The extent of these losses varies based on the specific technologies implemented and the pace of automation. Data from industry reports and expert analysis suggests a potential range of job losses.
Automation Level | Projected Job Losses (estimated percentage) | Illustrative Example |
---|---|---|
Partial Automation (e.g., automated guided vehicles, robotic systems for some tasks) | 15-25% | Ports implementing automated guided vehicles for transporting containers may reduce the need for some manual labor roles. |
Moderate Automation (e.g., fully automated container handling, driverless trucks) | 30-40% | A port transitioning to fully automated container handling systems, including driverless trucks, could see a substantial reduction in the number of dockworkers required. |
High Automation (e.g., fully automated port operations with minimal human intervention) | 40-60% | Ports adopting fully automated systems, with minimal human intervention, could see the most significant job losses. |
Potential Retraining Programs for Dockworkers
Effective retraining programs are essential to prepare dockworkers for the evolving demands of the automated port environment. These programs should focus on developing new skills and knowledge relevant to the new technologies and roles.
- Skills Enhancement Courses: Dockworkers need to develop proficiency in operating and maintaining automated equipment, as well as proficiency in data analysis and system monitoring. These skills will be critical for roles involved in operating and maintaining automated systems.
- Technical Training: Courses focused on programming, robotics, data analytics, and maintenance of automated systems will equip workers with the technical skills needed for the new roles.
- Upskilling Initiatives: Opportunities to transition into supervisory, management, or maintenance roles related to the automated systems are crucial. These positions will require different skill sets.
Economic Impacts of Automation on Ports
Automation in ports can lead to significant economic impacts, both positive and negative. The potential for increased efficiency and reduced operational costs is significant, but the costs of implementation and the need for retraining workers need to be considered.
Factor | Potential Positive Impacts | Potential Negative Impacts |
---|---|---|
Operational Efficiency | Reduced labor costs, faster turnaround times, improved cargo handling, and higher throughput | High initial investment costs for automation equipment, potential for disruptions during implementation. |
Productivity | Increased throughput capacity, enhanced safety measures, and improved reliability of operations. | Potential for job displacement, need for workforce adaptation, and potential for cybersecurity risks. |
Economic Growth | Increased port capacity, lower shipping costs, and improved trade competitiveness | Potential for economic inequality if workers are not adequately retrained, potential for increased reliance on foreign technology. |
Advantages and Disadvantages of Automation for Different Stakeholders
Automation in ports has varying impacts on different stakeholders. A thorough understanding of these impacts is crucial for a well-rounded assessment.
Stakeholder | Advantages | Disadvantages |
---|---|---|
Port Operators | Increased efficiency, lower labor costs, and higher productivity | High initial investment costs, potential for disruptions during implementation. |
Shipping Companies | Faster turnaround times, reduced shipping costs, and improved reliability | Potential for increased reliance on technology, and challenges in adapting to new systems. |
Dockworkers | Potential for new, higher-skilled roles, and increased safety measures | Potential for job displacement, need for significant retraining. |
Governments | Increased economic growth, improved trade competitiveness, and potential for new job creation in related industries | Potential for social unrest if job displacement is not addressed, potential for increased reliance on foreign technology. |
Conclusion
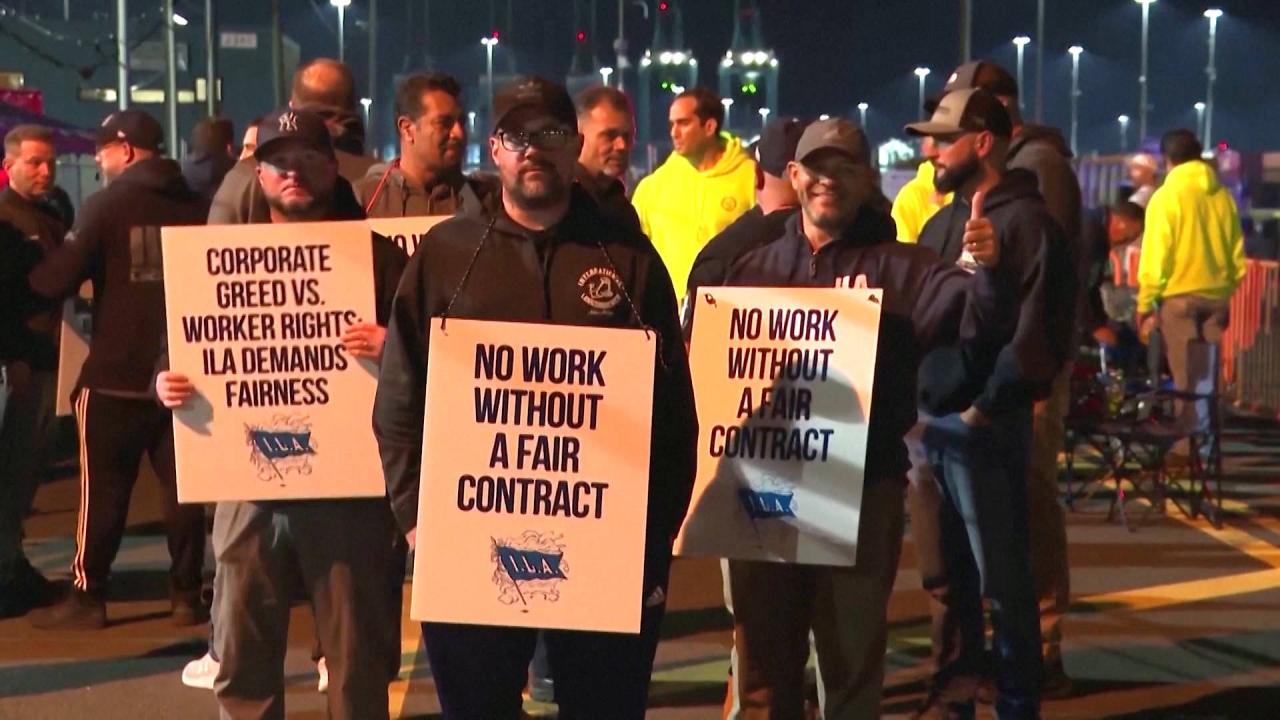
In conclusion, the impending dockworkers’ strike over automation underscores the need for proactive solutions. Addressing the concerns of dockworkers through retraining programs, transparent communication, and fair labor practices is crucial for mitigating potential disruptions and ensuring a smooth transition to an automated future. The potential for government intervention and industry-wide standards also warrants careful consideration. Ultimately, finding a balance between technological advancement and the needs of the workforce will be key to maintaining port efficiency and stability while protecting workers’ livelihoods.